What our welding services do differently.
We have multiple types of welding to accommodate many industry-specific parts and fabrication needs accurately. Our years of experience have allowed us to become advanced in welding techniques and skills. We work in Electronics, Medical Field, Aerospace, Oil & Gas, Energy, Transportation & Marinas, and Military & Defense. Further, we specialize in the complete welding and metal fabrication processes from start to finish. Large job or small job, we complete all your precision machining parts needs from concept and cutting, to surface treatments and delivery.
Quality American Manufacturing Craftsmanship
Don’t see your project get stuck in production – Proform American Manufacturing provides an accurate quote and reliable deadline. We work with you to cut production time, stay within your budget, and get the job done. Please pick up the phone and let our metal fabrication professionals help you with your project quote.
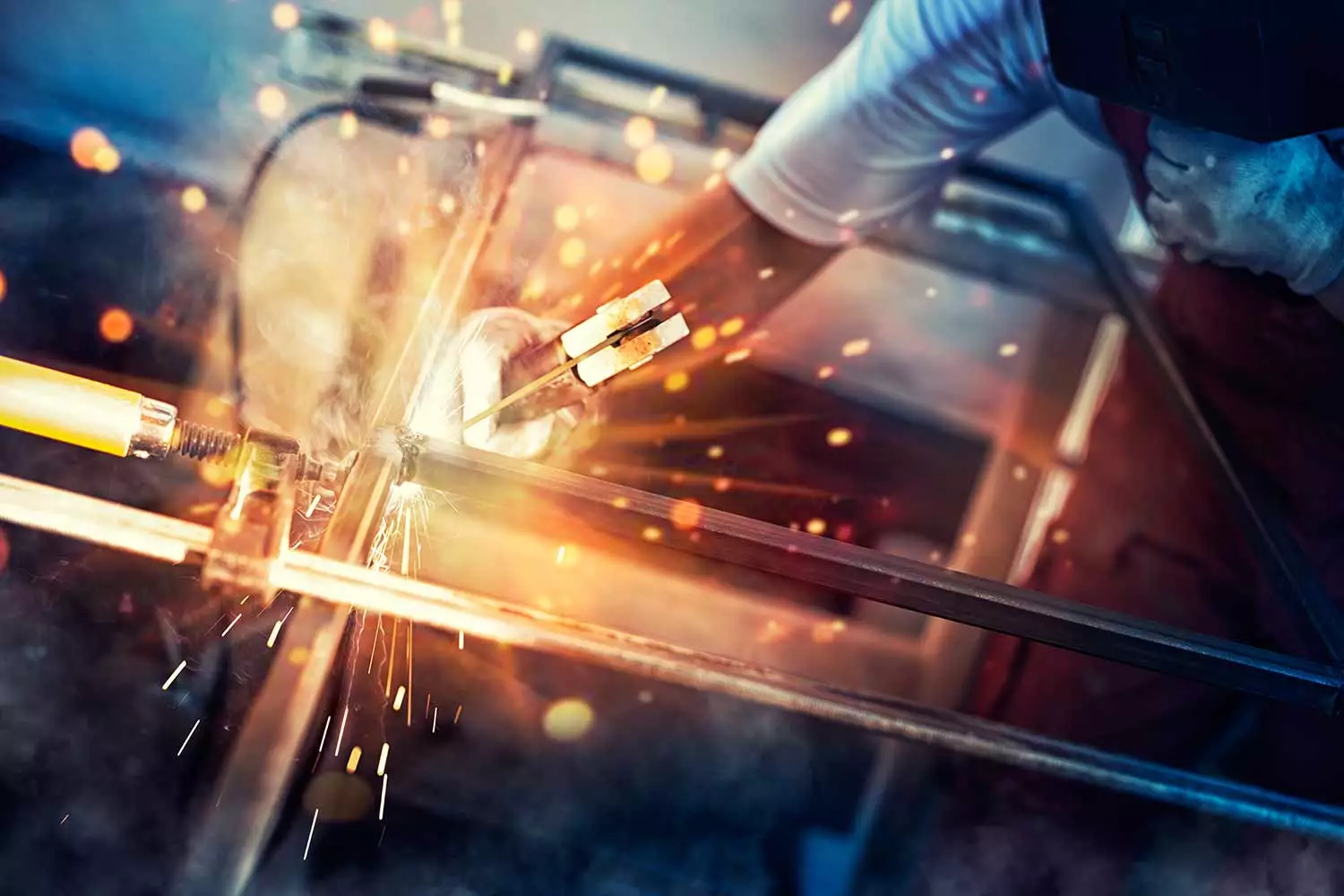
Keeping the Welding Project on Budget
In addition to welding, we offer many metal fabrication services. Some popular services include iron manufacturing, precision cutting & plasma cutting, surface treatments, and metal fabrication, among other things.
How does this all benefit you, our client?
Our volume production allows us to do large volumes of pieces quickly. Similarly, skilled artisans and automation further help to speed up production. Consequently, you experience reduced production time and lower costs. Therefore, when you consider how valuable time is, you get back to your client’s needs faster. Proform American Manufacturing is clearly an intelligent and cost-effective choice.
Welding strategies we employ.
Welding manufacturing has multiple methods that may be employed to get you the best results for your project. Each welding strategy has its advantages depending on your specific needs. Proform Manufacturing will work with you to find the best solution. We’ll go over solutions that fulfill the requirements of the project specs while also saving you time and money.
We effectively find the best satisfactory solution using our welding experience and the latest welding technology. Choosing the best welding technique depends on your project specs, intended use, material, industry requirements, budget, and time constraints.
Similar to MIG welding is flux cored arc welding. The difference being the metal filler has a core of flux. This core creates a gas shield around the weld. FCAW is a heavy and powerful weld most often used in structural welding. For this reason, Flux cored arc welding often uses hard metals, including carbon steel, cast iron, stainless steel, and hard-facing alloys. Contrarily, it will not use nonferrous metals and metal alloys.
Thicker metals often require the flux cored arc welding method. Not recommended for anything over 20 gauge, it is excellent for use on thinker metals. One of the benefits of FCAW is its efficiency in reducing waste. Moreover, it is often a low-cost option for customers using thicker metals on large jobs such as structural steel components. However, this method requires cleanup for a nicely fashioned weld appearance. One negative side of FCAW welding is its inability to use it with many pure metals such as aluminum, copper, lead, nickel, tin, titanium, and zinc.
SMAW uses a flux coated filler stick to create the weld. Due to its robust properties and no need for gas, this method is useful outdoors. Additionally, it is effective on rusted, painted, and dirty surfaces, making it ideal for repair welding. Another advantage is that skilled welders can swap out different types of electrodes for use on many other materials.
SMAW’s main benefit is its versatility. It also is useful in welding in both ferrous and nonferrous metal alloys. SMAW is also a low-cost welding method. Although the SMAW weld often has a less refined appearance than other welding procedures.
MIG stands for metal inert gas, and is also called gas metal arc welding (GMAW). The first thing to know about MIG welding is that it is a fusion welding process. Meaning it fuses two metals to form a singular hardened state. Fusion welding uses extreme heat to merge two or more metals at their melting point. The GMAW method often involves using a filler material. MIG welding feeds a constant consumable metal wire through the welding gun. The electrode reaches up to 6000 degrees Fahrenheit, thus welding the components together. Then, the consumable metal deposits into the base metal. These materials become a hardened state when they cool. GMAW is a highly reliable form of welding used for even the hardest metals.
MIG welding is a quick and reliable process, but don’t underestimate its skill level. MIG welding is suitable for various metals, including aluminum, copper, stainless steel, magnesium, and some steel, nickel, and iron properties. It is a versatile process available for different metal thicknesses. Also, the welding wand permits a preferred speed due to the continuous feed. When done correctly, professionals complete welding quickly and reliably. MIG welding provides a smooth tight weld.
TIG stands for tungsten inert gas and is another fusion welding technique. Similarly, GTAW methods see high-quality welding techniques used by highly trained welding technicians. The TIG welding approach uses a non-consumable Tungsten electrode, unlike MIG welding. It is one of the only forms of welding that can melt two metals together without filler metal. Yet, a filler wire, rod, or bar may be hand-fed on larger weld jobs to complete the weld.
The TIG welding method is suitable for almost all materials. With GTAW welding, a welding technician can weld as thin as 0.005-inch thick material. Hence TIG welding is ideal for many precision welding applications. A successful TIG weld has a clean appearance. Besides, GTAW welding has minor splatter and therefore does not require cleanup. Hence, the project moves quickly through to completion due to the absence of cleanup.
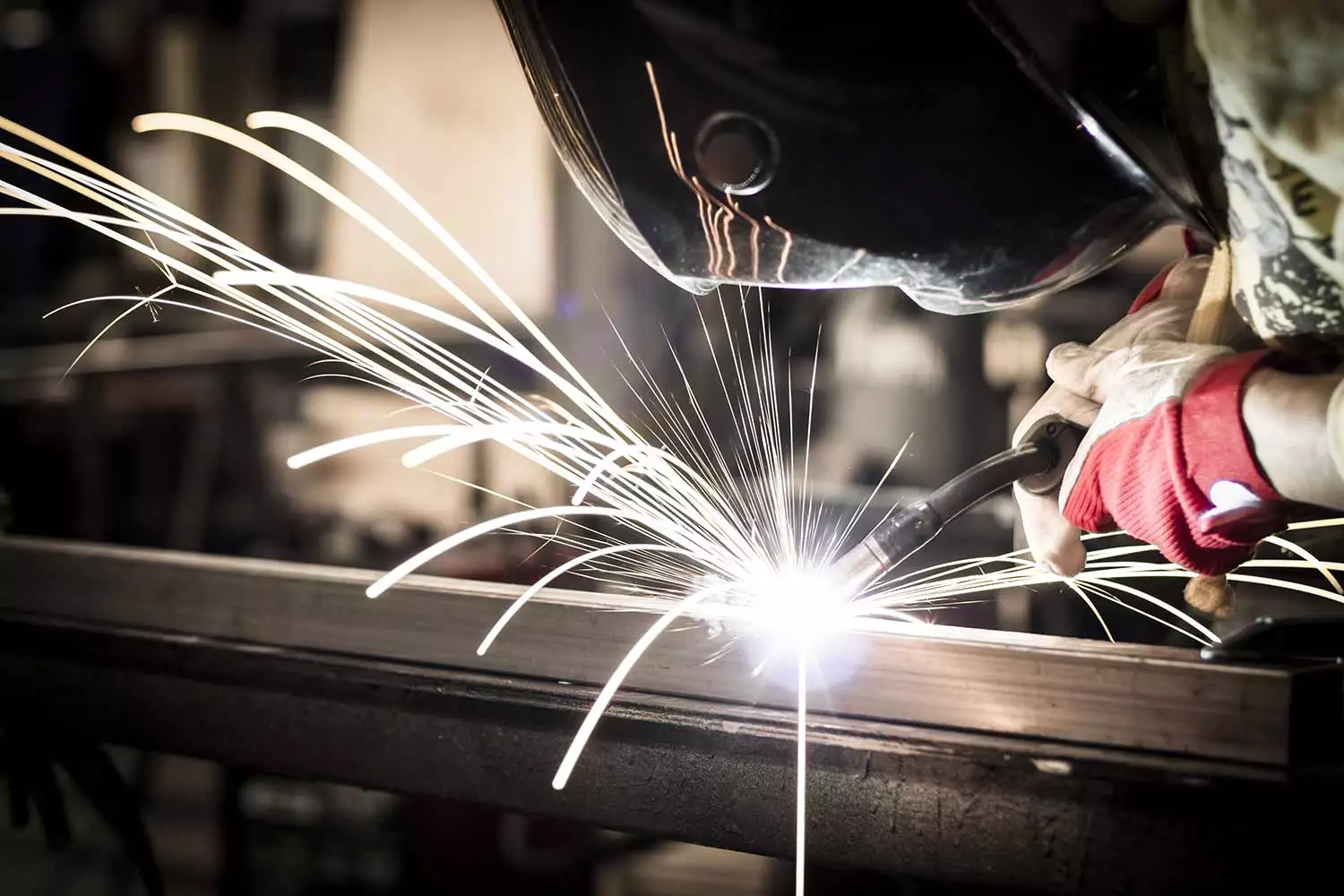
What is welding manufacturing?
When precision manufacturing calls for welding capabilities, our skilled artisans provide various welding manufacturing options from prototype to production. These different welding techniques allow us to accommodate many industries and materials.
Welding fabrication joins materials together.
The metals melt using concentrated high heat, pressure, or both, fusing them together permanently. After it cools, the fusion of metals often results in a stronger material than the original metal. Welding manufacturing is often vital in the metal fabrication process. Our professional welders are on staff. Additionally, each procedure is monitored closely for accuracy and weld appearance. Consequently, you’ll always get your metal part looking and performing at top levels and beyond expectations.
Precision welding with small parts.
Small parts require precision welding. MIG and TIG are precision welding methods often used in parts fabrication. For example, TIG welding yields precise welding manufacturing methods using metals as thin as 0.005-inch thick. Our skilled professionals know what process best suits your fabrication project. Not to worry, we have your precision parts task under control.
We often use flux cored arc welding or shielded metal arc welding for large-scale weldments. These two welding techniques are considered a more substantial welding process. For this reason, structural welding or heavy-duty equipment commonly uses FCAW and SMAW welding. We see these methods regularly used in industries like construction and large machining. Likewise, MIG welding is versatile in handling large metal fabrication projects in the transportation and manufacturing industries.
Are you looking for the highest quality welding manufacturing near you? Proform American Manufacturing provides Northeastern, IN, with premium welding services. Proform American Manufacturing handles your project with the care and precision details you’re looking to accomplish. Not only adapt in welding, but we also provide the highest quality in all your metal fabrication needs. Trust that we’ll see your project through from start to finish. Our experience and vast capabilities make us the right choice for your next parts fabrication job.
Our expert team identifies your needs and executes them with precision accuracy from the prototype to the delivery of high-volume orders. We focus on the attention to detail you’re looking to get when hiring a parts manufacturer. If you have a project requiring precision welding services, contact us today. Get quality parts done on your budget and your timeframe.
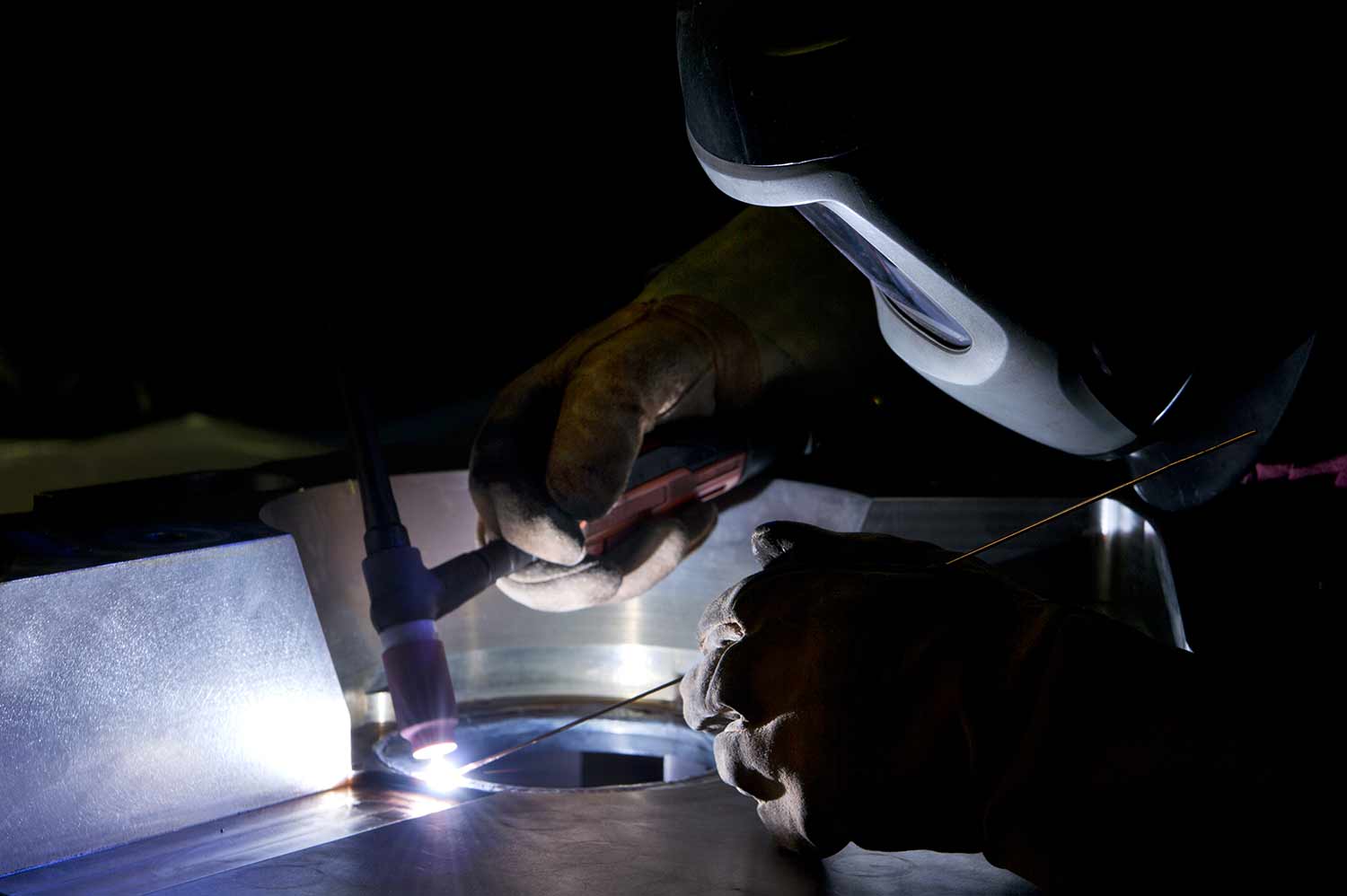