What is plasma cutting?
Plasma cutting is a metal fabrication process that cuts through metal using a concentrated jet of hot plasma. Plasma cutting is adept at cutting thick and thin materials alike. Because of its versatility, it is now taking on its counterpart of laser cutting.
The Highlight of Plasma Cutting
Plasma arc cutting is often faster than torch cutting. When combined with CNC automation machining, precision cutting is capable of smooth superior angular geometric curves and shapes.
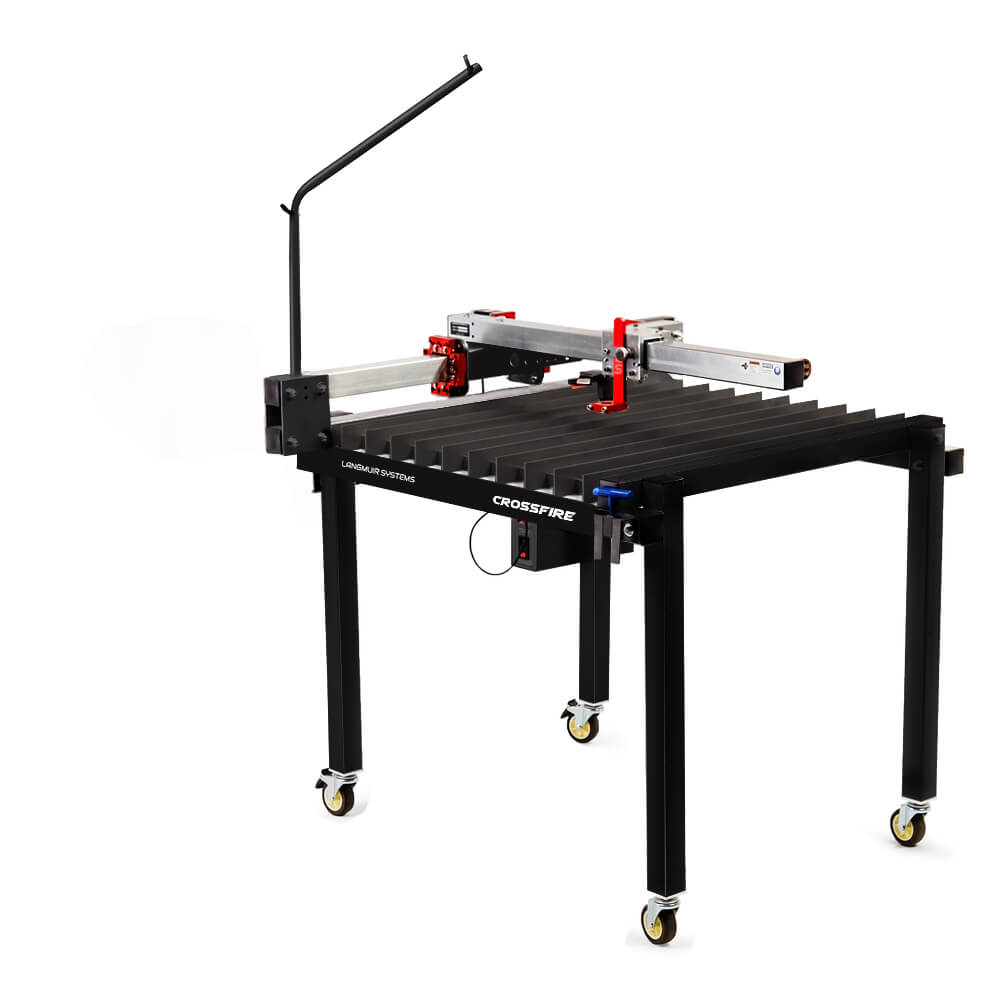
How does plasma cutting work?
A jet of highly heated plasma, ionized gas, is concentrated into a fine stream of gas used to cut through metal. Plasma cutting is a thermal cutting technique, which means that it uses heat to cut the metal. In this case, a plasma jet sends a stream of hot plasma that cuts electrically conductive materials.
Plasmas are the fourth state of matter. The three most commonly known forms of matter are solid, liquid, and gas. Yet, the fourth state of matter does exist. Often overlooked, plasma, known as the fourth state of matter, is very resourceful in metal fabrication.
What metals can a plasma cutter cut?
Common metals that a plasma cutter will penetrate include steel, stainless steel, aluminum, copper, brass, and non-ferrous metals. Proform American Manufacturing’s plasma cutter slices through 3/4 inch thick metal.
Often fabrication shops use a plasma arc cutter because of its faster cutting speed and precision cutting ability. These qualities are beneficial to metal fabrication because they keep the costs down while providing good cut quality. Therefore, plasma cutting is quickly advancing in the industry for these reasons.
Plasma cutting machine operations are widely used, from industrial CNC plasma operations to smaller-scale individual shops.
When it comes to sheet metal cutting, plasma cutting gets its opportunity to shine. The focused nozzle produces a scorching localized plasma stream. The narrowed steam easily cut curves and angles that otherwise may be problematic with other metal fabrication processes.
Conversely, iron, lead, tin, and tungsten are some metals that do not conduct electricity well. These metals are, therefore, non-conducive to this cutting method. Non-conductive metals use other metal cutting techniques. Proform American Manufacturing is skilled at cutting all types of metal materials. Proform also performs iron manufacturing techniques to manipulate iron fabrication in diverse ways.
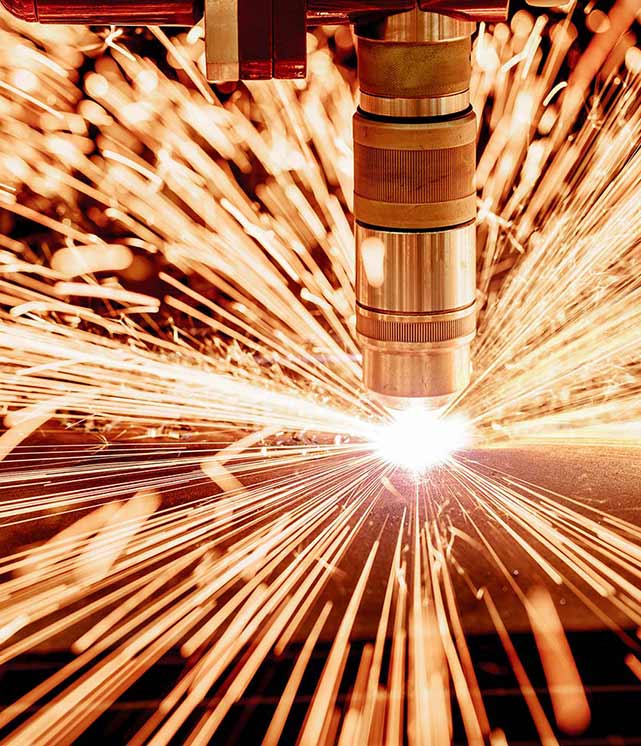
CNC Plasma Cutting Table
A 2-axis plasma cutting service gives the material a 90-degree cutting edge against the cutting material. It is most commonly used for sheet metal to produce flat cuts in metal up to 3/4 inch thick. The 2-axis method moves along the x and y axes.
On the other hand, 3-axis plasma cutting introduces the addition of the z-axis. Doing so allows the cutting nozzle, which is usually at 90 degrees, the ability to tilt. Tilting provides a new cutting angle other than 90 degrees. Creating an angled edge is generally preparing for a welding application in metal fabrication. But, the application of the third axis doesn’t end there. Angular cutting capability also creates countersunk holes and chamfer edges as well as angled milling slots.
Finally, tube and pipe cutting often keep the nozzle head stationary on the cutting table. A cutter feeds the pipe through the machine rotating the metal pipe or tube. The plasma arc electrode nozzle stays stationary as the desired cutting takes place on the rotating object below.
Precision CNC Plasma Cutting
CNC (Computer Numerical Control) technology controls the path of the plasma torch via computer programming. Having a computerized cutting path further allows precise controls over the cut quality. Using computer-aided technology system parameters adjust with only a few mouse clicks. Each metal, carbon steel, stainless steel, aluminum, copper, brass, and non-ferrous metal, contains specific production parameters based on the element’s characteristics. Along with this, the fabricator must also consider the thickness of the metal.
As the materials change, details in the cutting parameters must also change. For example, the feed rate, pierce delay, pierce height, and gas mixture, to name a few. Such details are automated to speed up the process when using a CNC plasma cutting machine. Furthermore, automation reduces the risks of human error during recalibrations to the machine and the plasma arc flow.
Do you have tiny precision parts that cutting with plasma is not equipped for?
Not to worry, Proform American Manufacturing professionals excel in Swiss-style machining also. Proform’s fabrications processes execute large and small projects alike. Skilled artisans manage every step of your manufacturing process. Visit our metal fabrication page to learn more.
Benefits of Plasma Cutting
Plasma cutting is ideal for sheet cutting. Also, this unique cutting form has the ability to cut metal materials stacked on top of one another.
User benefit = Customers gain the ability to produce complex parts in the metal of their choice.
The thickness of the material further determines the cutting speed. Consequently, thinner materials decrease the cutting time, reducing overall project timelines. As thickness decreases, research shows high-performance plasma cutting reaches speeds up to 12 times faster than oxy fuel cutting.
User benefit = Manufacturing more parts in less time reduces the project timeframe and costs.
Moreover, the CNC plasma cutter has a high repeatability rate for accuracy. It creates precision machining parts effectively, quickly, and repeatedly without error. A finished part may still require welding or finishing services but quality cuts often reduce other service needs.
User benefit = It gives superior quality parts with improved operations and increased productivity through design.
User benefit = Safety factors often figure into the cost of a project. Thus without significant safety risks, prices may remain lower for the consumer.
What industries are best suited to plasma cutting?
Fabrication shops often see plasma cutting as most beneficial to the automotive, aerospace, electrical equipment, and industrial industries. The popularity in these sectors is most likely due to two factors. First, these industries often have long cutting curves. To ensure smooth precision along a curve, it’s best to perform the cutting action without starting and stopping. The second prominent factor for these industries is their high use of sheet metals fabrication needs. Plasma cutting fills both of these main criteria exceptionally well. However, Proform American Manufacturing has used plasma cutting for multiple industries and innovative project solutions.